Why Implement the 5S Method?
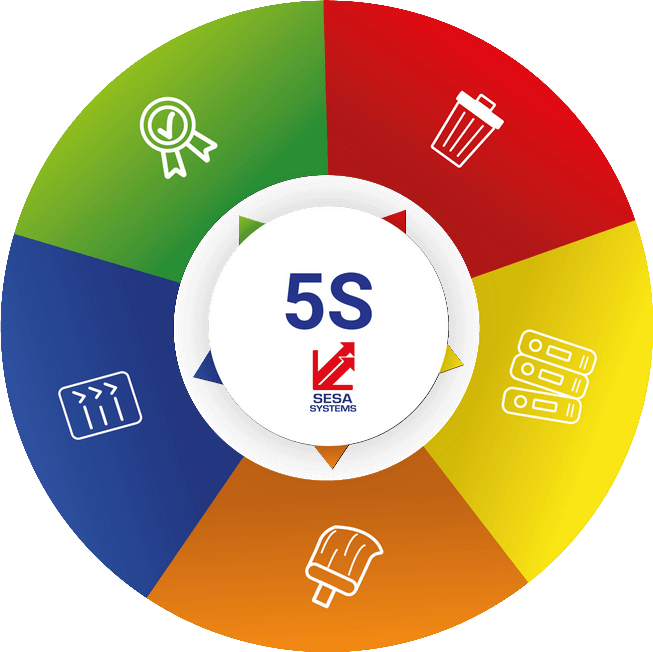
The 5S method, originating from Japan, is a systematic approach designed to organize workspaces efficiently and safely. This cornerstone of LEAN Management is divided into five stages — Seiri (Sort), Seiton (Set in Order), Seiso (Shine), Seiketsu (Standardize), and Shitsuke (Sustain) — providing a strong foundation for continuous improvement and operational performance. But why should companies adopt the 5S approach? Here are the main reasons why implementing this methodology is beneficial.
Boosting Productivity
One of the most immediate advantages of the 5S method is increased productivity. By eliminating unnecessary items (Seiri) and optimally organizing those that remain (Seiton), employees spend less time searching for tools, materials, and objects needed for their tasks. When everything is in its place, it’s easier to navigate. This organization reduces downtime and ensures more efficient use of resources. For instance, in a manufacturing plant, a well-organized workshop allows workers to move quickly between workstations, significantly improving overall output.
Reducing Risks and Accidents
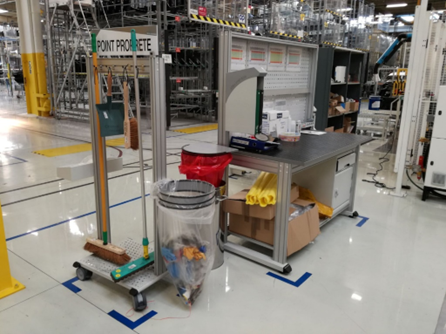
A clean and organized workspace is less prone to accidents. The third S, Seiso, emphasizes regular cleaning of work areas and stations, which not only maintains a pleasant environment but also prevents potential injuries. Clutter and misplaced tools can cause accidents; removing these hazards protects employees’ health and minimizes interruptions caused by incidents.
Enhancing Quality
Process standardization (Seiketsu) is crucial for maintaining high quality standards. By applying uniform procedures, variations and errors are minimized. This ensures that every product or service meets consistent quality criteria, enhancing customer satisfaction and strengthening the company’s reputation. For example, in an automotive assembly line, standardized procedures ensure that every vehicle is built with the same precision and equipment.
Increasing Employee Engagement and Motivation
Involving employees in the 5S process can greatly enhance their engagement and motivation. When they actively participate in organizing and improving their workspace, they feel more responsible and valued. This engagement is particularly critical during the Shitsuke phase, where discipline and ongoing training ensure the sustainability of improvements. Engaged employees tend to be more productive and less likely to be absent, which directly benefits the organization.
Reducing Costs
Implementing the 5S method can lead to significant cost reductions. By optimizing space and resource usage, companies can eliminate unnecessary expenses. For example, well-managed inventory reduces waste and overstocking, leading to savings in storage and inventory management costs. Additionally, accident prevention reduces expenses related to downtime and employee compensation.
Creating a Pleasant Work Environment
A clean, organized, and safe workspace also contributes to employees’ overall well-being. An orderly and clean environment is more enjoyable to work in, improving morale and job satisfaction. The 5S method also fosters communication and collaboration among teams by creating a setting where improvement ideas are shared and collectively implemented.
Conclusion
In summary, the 5S method is a powerful strategy for improving productivity, quality, safety, and employee well-being within an organization. By adopting this systematic approach, companies can create more efficient, safer, and enjoyable work environments. Tangible benefits, such as cost reductions and quality improvements, combined with intangible advantages like increased employee engagement, make the 5S method an essential tool for any organization striving to enhance its overall performance.