How to Train and Raise Awareness Among Your Teams About the 5S Method?
The 5S method, derived from Lean Manufacturing, is essential for establishing an efficient, secure, and well-organized work environment. Equally applicable to office and production settings, it is based on five Japanese principles: Seiri (Sort), Seiton (Set in Order), Seiso (Shine), Seiketsu (Standardize), and Shitsuke (Sustain). For a company like SESA SYSTEMS, specializing in Lean Manufacturing, it is crucial to provide tools to implement this methodology across various organizations and offer guidance on how to best raise team awareness to maximize work quality and productivity. Here are the steps you can follow to achieve this.
Explain the Fundamentals of the 5S Method
Start with a comprehensive introduction to the 5S method. Use visual aids and concrete examples to illustrate each step. For instance, a demonstrative video showcasing a workspace before and after implementing the 5S principles can be very impactful. Explain how each principle contributes to the overall improvement of the workplace and process efficiency.
- Seiri (Sort): Remove unnecessary items from the workspace.
- Seiton (Set in Order): Organize necessary items in an orderly manner.
- Seiso (Shine): Regularly clean and inspect equipment.
- Seiketsu (Standardize): Establish routines and standards.
- Shitsuke (Sustain): Maintain and continuously improve practices.
Train Teams On-Site
Practical training is key. Organize interactive workshops where teams can apply the 5S principles in real-life scenarios. Start with a pilot area and demonstrate how each step can be implemented. Encourage active participation and allow employees to experience the immediate benefits of the method.
Provide Suitable Tools and Products
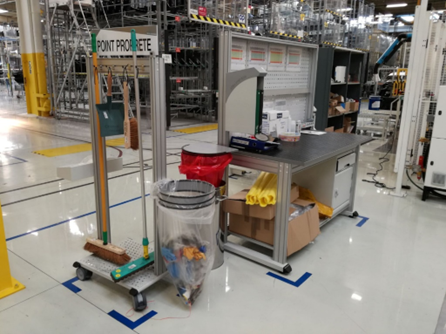
Equip your teams with the right tools to support the 5S implementation. For example, SESA SYSTEMS offers signage boards, storage trolleys, and cleaning kits tailored to this purpose. Ensure that teams understand how to use these tools effectively to optimize their workspaces.
Foster a Culture of Continuous Improvement
The 5S method is not a one-time task but a continuous process. Encourage employees to embrace a culture of ongoing improvement. Hold regular meetings to discuss project management, progress, challenges, and new ideas for improving practices. Utilize dashboards and performance indicators to track progress and motivate teams.
Acknowledge and Reward Efforts
Recognizing efforts and achievements is critical to maintaining team engagement. Implement a reward system for employees who show exemplary commitment to the 5S principles. This could include certificates, bonuses, or special mentions during team meetings.
Communicate Effectively
Clear communication is vital for raising awareness about the 5S method. Use multiple communication channels to disseminate information: newsletters, posters, meetings, and internal digital platforms. Ensure the importance of 5S is conveyed clearly and consistently at all organizational levels.
Regularly Evaluate and Adjust
Continuously evaluate the effectiveness of 5S implementation. Conduct internal audits to identify strengths and areas for improvement. For example, you can use the SESA CHECK application for this purpose. Be prepared to adjust strategies based on team feedback and field observations. The goal is to make 5S a natural element of your corporate culture.
Key Takeaways
Raising team awareness about the 5S method is a strategic step for any company aiming to enhance efficiency and workplace environment. By following these steps, your organization can ensure a successful implementation of the 5S methodology, resulting in significant improvements in productivity, safety, and employee satisfaction. Adopting 5S is an investment in a better future for both the company and its workforce.