How to Optimize Order Preparation and Packaging with the PACKINGPOST Range?
Optimizing order preparation and packaging in warehouses is a crucial goal for companies aiming to enhance logistical efficiency and reduce operational costs. Achieving this requires a methodical approach, proper workspace organization, and adequate staff training. Here are some strategies to reach this goal.
Organize Your Space Effectively
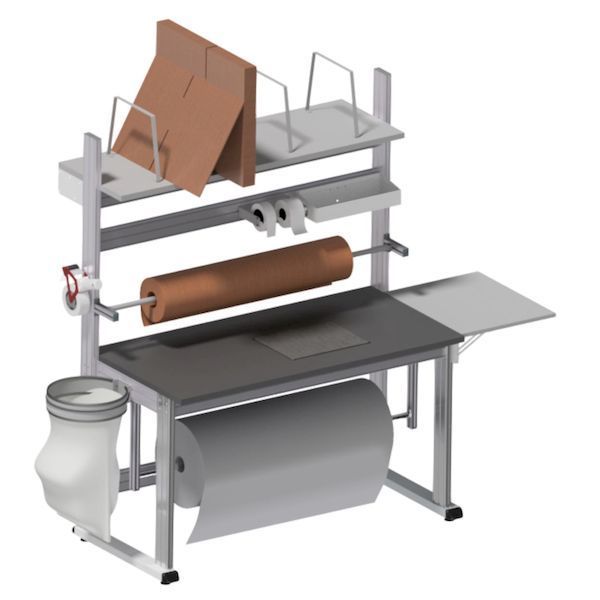
The first step involves the physical organization of packaging workstations. Their positioning relative to goods and storage areas is essential. A well-planned layout minimizes unnecessary operator movement between picking locations and packing stations, creating an optimized pathway that boosts productivity. Following ergonomic principles and the 5S methodology for workspace arrangement helps ensure that employees have easy access to necessary tools, references, and materials. For example, placing frequently used items within reach and organizing packing zones in a logical flow (receiving, packing, shipping) can significantly speed up the process. The PACKINGPOST range was developed precisely with this in mind, offering packers easy access to boxes and other packaging materials.
Standardize Procedures
Standardizing packaging processes is also critical. By establishing clear and consistent procedures, companies can ensure quality and reduce variability. Checklists and specific protocols should be developed for each type of order and product. These procedures can even be displayed on PACKINGPOST stations to facilitate order preparation management. Automated conveyor systems or dynamic shelving, for example, can transport products between different stations without human intervention, reducing both time and effort.
Train Operators
Staff training is another key aspect of optimizing packaging stations. Employees need to be trained in best practices for preparation and packaging. From receiving to shipping, and including picking and packing, regular training sessions and updates on procedures help maintain high levels of skill and adaptability. Training games can be used to ensure engagement and comprehension. Involving employees in continuous improvement efforts is also beneficial, as they can offer suggestions based on daily experience.
Monitor Your Metrics
Finally, regular performance evaluation and analysis are essential to identify improvement opportunities. Key performance indicators (KPIs), such as order preparation time, error rates, and productivity per station, should be closely monitored. Analyzing this data helps identify bottlenecks and adjust processes as needed. Feedback and internal audits are also valuable tools for refining strategies and enhancing overall efficiency.
Key Takeaways…
To optimize order preparation and packaging with workstations like PACKINGPOST, companies should take a comprehensive approach that combines ergonomic organization, process standardization, staff training, and ongoing performance evaluation. By applying these principles, companies can not only improve operational efficiency but also deliver better service to their customers, strengthening their competitive edge in the market.