What is the Purpose of LEAN?
The LEAN concept, initiated by Toyota in the 1950s, has become a cornerstone for efficient operations and resource management across various industrial and organizational fields. Whether in manufacturing (LEAN Manufacturing), administrative services (LEAN Office), or business management (LEAN Management), LEAN and its methods aim to minimize waste while maximizing value for the customer. Its main goal is to optimize organization and each key process step by eliminating non-essential activities, reducing delays, and enhancing the quality of products or services offered through a precise methodology. By utilizing these tools, teams become more effective, which boosts both the competitiveness of the company and its management. With over 30 years of experience, SESA SYSTEMS has evolved alongside the needs of businesses, offering innovations to implement this philosophy effectively.
LEAN Manufacturing: A Philosophy Adapted to Production Workshops
In the context of LEAN Manufacturing, the primary objective is to achieve a smooth and efficient production line capable of quickly responding to market demands while keeping costs low. To accomplish this, the LEAN system is implemented within the company to eliminate waste such as overstocking, waiting times, unnecessary movements, and production defects. By fostering a culture of continuous improvement, companies adopt practices like Kaizen (continuous improvement), Just-in-Time (JIT) to minimize inventory, and Jidoka for early defect detection. For optimal efficiency, every employee in the company must actively participate in these performance optimization methods.
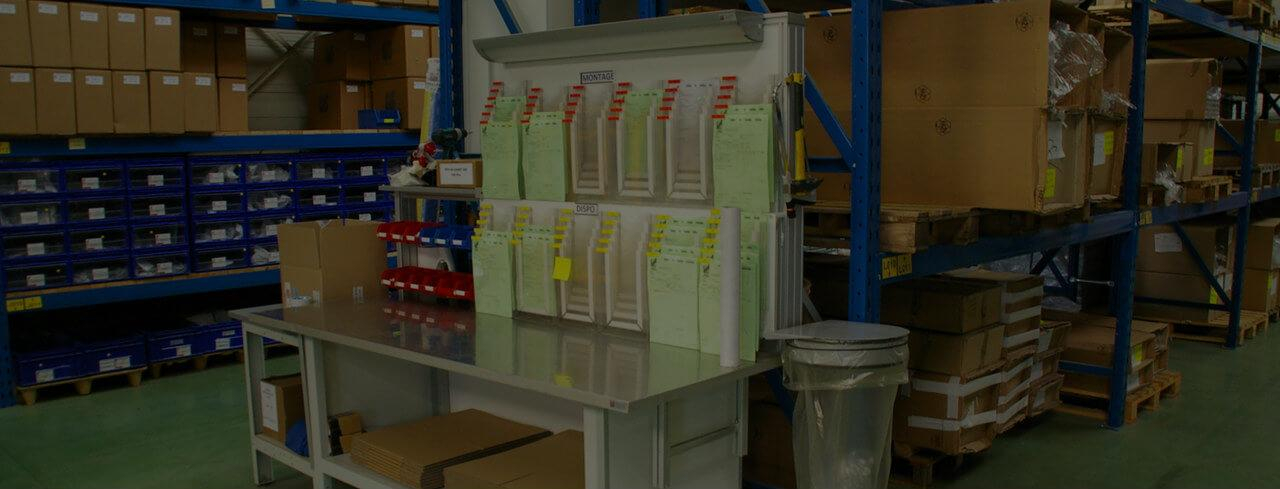
LEAN Office: The LEAN Approach for Office Environments
In an office setting, LEAN Office aims to streamline administrative processes and improve workflow. The goal is to smooth operations by removing unnecessary tasks, delays, and errors that can slow productivity and impact service quality. To achieve this, companies apply techniques like 5S to organize workspaces, Value Stream Mapping to identify value streams, and Kanban for visually and effectively managing tasks and projects.
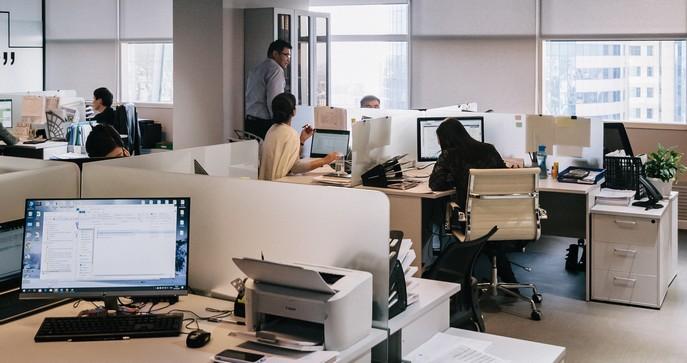
LEAN Management: A Concept Designed for Optimized Business Management
As for LEAN Management, its objective is to adopt a people-centered and participatory management approach to enhance human resources and decision-making processes. The goal is to create a work environment where employees are encouraged to actively contribute to operational improvements and problem-solving. LEAN Management principles emphasize the delegation of responsibilities, continuous training, participatory leadership, and open communication to foster employee engagement and achieve organizational goals.
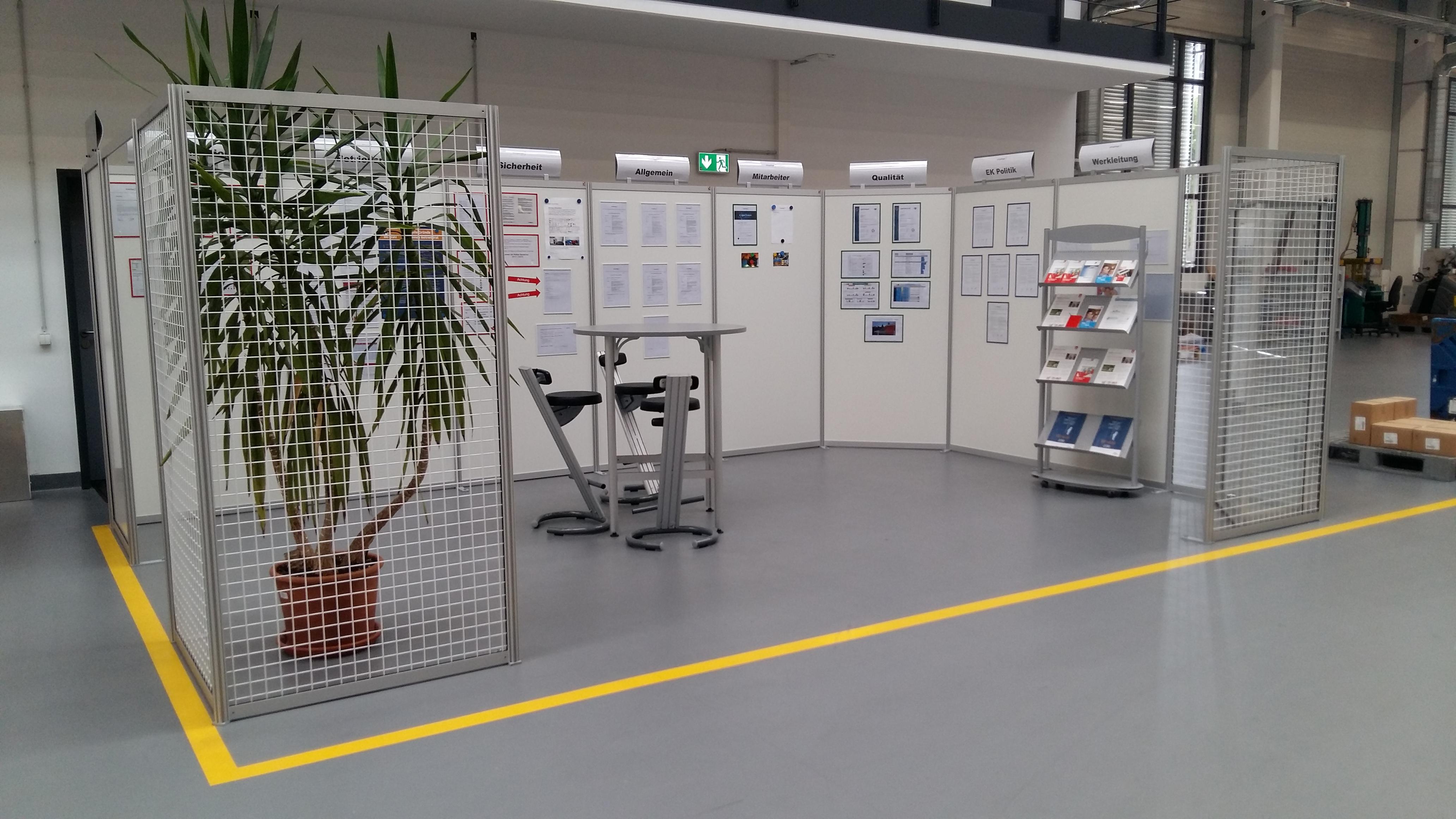
Key Takeaways
In summary, the purpose of LEAN, whether it’s LEAN Manufacturing, LEAN Office, or LEAN Management, is to create customer value while eliminating waste and optimizing processes and resources. By adopting a systematic approach focused on continuous improvement, companies can increase their competitiveness, profitability, and adaptability to market changes. LEAN thus becomes a driver of organizational transformation, promoting efficiency, quality, and the satisfaction of both customers and employees.