How to Organize a Continuous Improvement Process in a Company with LEAN?
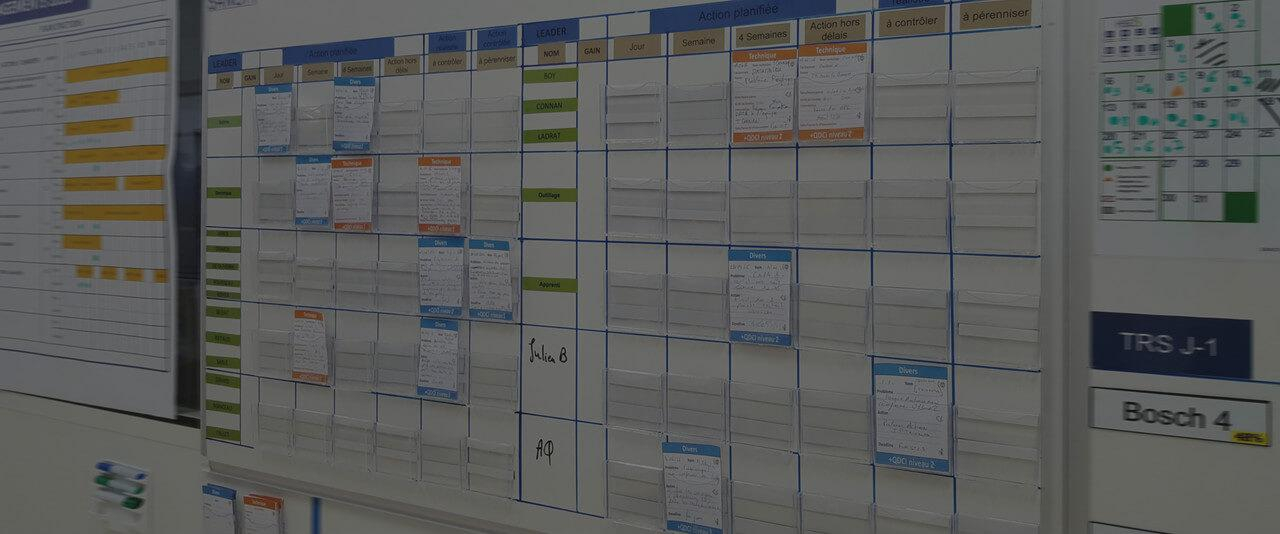
Continuous improvement is a fundamental pillar of effective business management. LEAN Management (and LEAN Manufacturing), inspired by Toyota’s production principles, provides a structured approach using various methods to optimize processes, reduce waste, solve problems, and enhance quality. Organizing a continuous improvement process using LEAN methodology requires a deep understanding of its core principles and a methodical implementation. With a well-thought-out action plan, you can start seeing initial gains fairly quickly. Here are the main steps to follow:
1. Understanding LEAN Principles
To implement an improvement process, it is crucial to grasp LEAN’s fundamental principles. These principles include creating customer value, identifying and eliminating waste, optimizing workflow, and fostering continuous employee involvement in process improvement. For a more comprehensive understanding of LEAN’s system, methods, and philosophy, consider consulting resources such as SESA SYSTEMS articles dedicated to these topics.
2. Analyzing Current Processes
The first step in organizing an improvement initiative is to analyze the company's current processes. This involves mapping workflow, identifying areas of waste, and understanding bottlenecks. A thorough analysis helps target priority areas for improvement.
3. Defining Improvement Objectives
Once gaps are identified, setting clear, measurable improvement goals is essential. These goals should align with the company’s overall strategy and focus on creating customer value, such as reducing cycle times, improving quality, or lowering costs.
4. Employee Engagement
Employee involvement at all levels is crucial to the success of any improvement process. LEAN encourages active participation across the organization, valuing everyone’s ideas and input. Organizing brainstorming sessions, working groups, and LEAN training can help engage and motivate employees.
5. Implementing LEAN Tools
Once goals are defined and employees engaged, it’s time to implement LEAN tools to improve processes. This might include techniques such as Kaizen (focused on continuous improvement), 5S (for workplace organization), Kanban (for visual workflow management), or SMED (for reducing setup times). Each tool is tailored to the specific needs of the business and helps create an environment focused on efficiency and quality.
6. Measuring and Monitoring Progress
Measuring and tracking progress is essential for evaluating the effectiveness of implemented initiatives, identifying successes and challenges, and adjusting strategies accordingly. Key performance indicators (KPIs) can be used to monitor results and ensure that improvement goals are being met.
7. Replication and Continuous Integration
Once a successful improvement initiative has been implemented in a specific area, it’s important to replicate best practices across other parts of the organization. LEAN is built on a culture of continuous improvement, where lessons learned are integrated throughout the company to create lasting transformation.
Key Takeaways
Organizing a continuous improvement process in a company using LEAN requires long-term commitment, a solid understanding of LEAN principles, and active employee collaboration. By following a methodical approach, setting clear goals, and using the right tools, companies can foster an environment where efficiency, quality, and innovation thrive. This enables the company to offer higher quality products and more value-added services to its customers.