How to Implement the Kanban Method in 5 Steps?
The Kanban method, initially developed by Toyota as part of its production system, has expanded beyond the automotive industry to become a widely-used approach in various sectors, including office environments, non-manufacturing settings, and the service industry. Implementing the Kanban method in these contexts requires a clear understanding of its core principles and thoughtful adaptation to the specific needs of each environment. Here are the essential steps to apply the Kanban method effectively in both industrial and office settings.
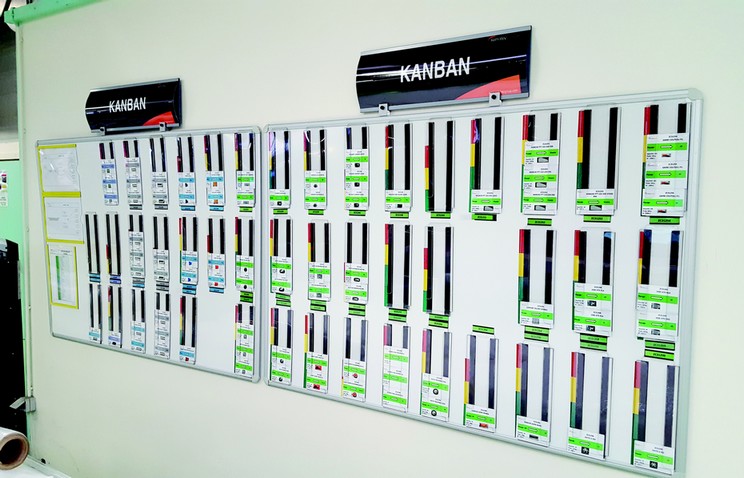
Step 1: Identify Key Workflows and Processes
First, it’s crucial to grasp the fundamental principles of the Kanban method. At its core is the concept of visual workflow management. This involves breaking down this flow into small, visual tasks, or "cards," which are then placed on a Kanban board. This board is typically divided into columns representing different stages in the process, such as "To Do," "In Progress," and "Completed." Each task moves through these columns as it progresses, providing a clear visual representation of work status.
Step 2: Organize Key Workflows on a Board
In industrial settings, implementing the Kanban method often starts by identifying existing workflows and mapping out key processes. This helps pinpoint bottlenecks and areas for improvement. Once workflows are understood, physical Kanban boards or new digital tools can be used to visually represent these processes. Each stage of the workflow is represented by a column on the board, and Kanban cards move through these columns as work progresses.
In office environments, the Kanban method can be similarly applied, but tailored to office-specific tasks and workflows, such as project management, team coordination, or individual task management. For example, in software development, Kanban-adapted methods like Agile or Scrum can be used. Additionally, task management software or online Kanban tools can facilitate the creation of virtual Kanban boards to efficiently track and manage office work.
Step 3: Measure and Control Work in Progress (WIP)
A key aspect of the Kanban method is limiting work in progress (WIP). This means that at each stage of the process, only a specific amount of work is allowed to be active at a time. This approach helps prevent work overload and maintain a steady workflow. By setting and enforcing suitable WIP limits, both in industry and office settings, teams can improve efficiency and ensure timely delivery of work.
Step 4: Schedule Progress Meetings
Communication and collaboration are also essential for a successful Kanban implementation. Encouraging transparency and fostering open communication within the team allows obstacles to be quickly identified and issues to be proactively resolved. Regular Kanban review meetings can be held to discuss work progress, address potential issues, and make adjustments to the process as needed.
Step 5: Adjust and Rebalance Work as Needed
Finally, it’s important to understand that Kanban is an evolving process. Teams should be open to experimentation and continuous adaptation of their Kanban system to respond to changing work conditions and customer needs. By monitoring process performance and gathering team feedback, adjustments can be made to continually improve work efficiency and quality.
Visual Workflow Management: The Heart of the Kanban Method
In conclusion, with the right tools and an understanding of core principles, the Kanban method can be implemented in both industrial and office settings. By adapting Kanban techniques intelligently to each environment and fostering teamwork and adaptability, organizations can achieve enhanced visual workflow management, reduced bottlenecks, and overall operational efficiency.