How to Complete a PDCA Cycle?
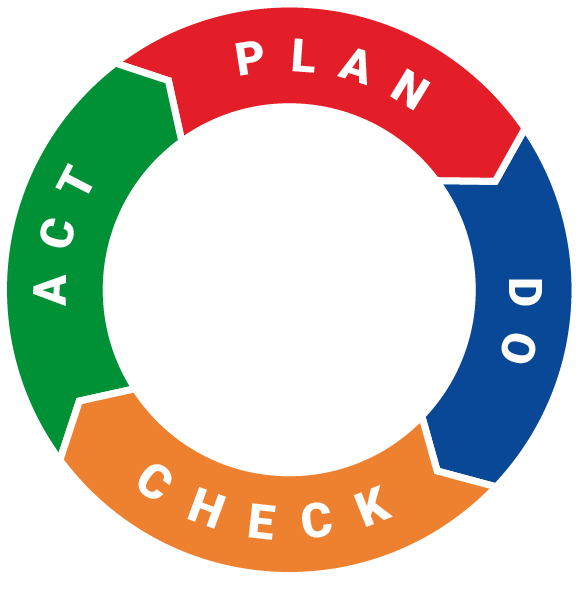
The PDCA cycle (Plan-Do-Check-Act), also known as the Deming Wheel, is an iterative Lean method for quality management and continuous improvement. This means that each completed step leads to the next, in a cycle that repeats iteration after iteration. This structured approach enables businesses and organizations to systematically improve their processes. Here is a step-by-step guide, based on SESA SYSTEMS' recommendations, to successfully implement a PDCA project in your organization.
Plan
The first step in the PDCA model is planning. This involves setting objectives and designing a framework to achieve them. This stage includes analyzing the current situation, identifying problems, and formulating potential solutions.
- Define the Objective: Start by determining what you want to improve. Remember to set realistic goals following the S.M.A.R.T. principle, meaning that objectives should be Specific, Measurable, Achievable, Relevant, and Time-bound.
- Analyze the Situation: Gather data on the current process to understand its performance and identify the root causes of problems and potential areas for improvement.
- Develop an Action Plan: Identify the specific actions needed to meet the objectives. This may include modifying existing procedures, introducing new techniques, implementing new processes, or training staff.
- Allocate Resources: Determine the necessary human, material, and financial resources needed to execute the plan.
Do
The second step involves implementing the framework developed. This is an execution phase where solutions are tested on a small scale.
- Implement the Plan: Execute the planned actions in a pilot area or on a small scale to minimize risks. Be mindful of adhering to the scheduled timeline for this testing phase.
- Train and Inform Staff: Ensure that the entire team and all stakeholders understand the plan and know what is expected of them.
- Collect Data: During implementation, gather data to assess the impact of the actions undertaken.
- Monitor Closely: Closely track progress to quickly identify any issues or deviations from the plan.
Check
The third step is verification, which involves comparing the results achieved with the objectives set to evaluate the plan's effectiveness.
- Analyze Results: Compare the data collected during the implementation phase with the established objectives. Statistical tools can be used to analyze the results. For example, you could compare the defective parts produced over a certain period before and during the test phase to evaluate the relevance and performance of the plan.
- Evaluate Discrepancies: Identify gaps between expected and actual performance. Analyze the causes of these gaps to understand why some actions were successful while others were not.
- Gather Feedback: Obtain feedback from employees and other stakeholders on their implementation experience.
Act
The final step is to act based on the results of the verification phase. This usually involves adjustments or scaling up the tested and validated solutions.
- Standardize Successes: If the plan was successful, integrate the changes into regular work procedures and document them.
- Implement Improvements: If problems were identified, make the necessary adjustments and plan a new PDCA cycle to continue improving.
- Share Results: Communicate the results and lessons learned across the organization to promote a culture of continuous improvement.
- Plan the Next Cycle: Use the insights from this cycle to plan the next one, targeting other areas of the process for improvement.
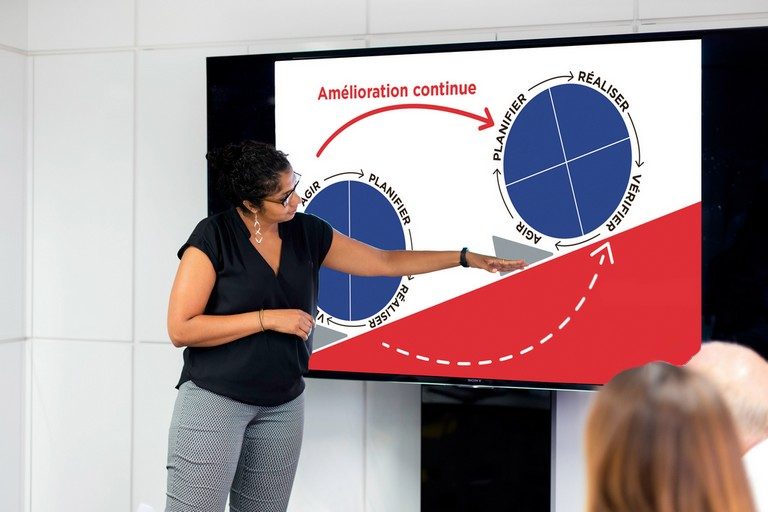
Key Takeaways
In summary, the PDCA cycle is a powerful tool for any organization aiming to continuously improve its processes and enhance the quality of its products or services. By systematically following the PDCA steps (Plan, Do, Check, Act), companies can not only solve existing problems and optimize processes but also prevent future issues. The success of this method lies in clearly defining objectives, a commitment to rigor and constant improvement, and the active involvement of all stakeholders.