How to Improve Efficiency through LEAN Management
In an era of intensified competition, companies are constantly seeking ways to enhance their operational efficiency to stay relevant in their markets. LEAN Management emerges as a powerful strategic approach, offering methods, tools, and principles for optimizing processes, reducing waste, and increasing added value. Understanding and establishing an action plan to implement LEAN Management can fundamentally transform how a company operates, allowing it to navigate a continuously evolving environment more smoothly.
What is LEAN Management, and What are Its Principles?
LEAN Management originated in the management practices developed by Toyota in the 1950s. At the time, the initial goal was to minimize resource waste while maximizing value creation for the customer—in other words, optimizing the company's overall flow. Since then, this approach has been adopted and adapted worldwide, becoming a pillar of modern management.
1. Developing a Holistic Approach
To effectively implement LEAN Management, it’s essential to follow several key principles. First, adopting a holistic approach by examining the entire system rather than individual parts is crucial. This often requires a shift in mindset, as companies must move from a fragmented view focused on specific departments to a comprehensive view of their operations—considering the company as a whole.
2. Waste Elimination
A core principle of LEAN Management is waste elimination. These wastes, referred to as "muda" in Japanese, can take various forms: overproduction, delays, unnecessary transportation, excessive inventory, unnecessary movements, overprocessing, and defects. By identifying and eliminating these sources of waste, companies can streamline their operations and improve overall efficiency. For more on this, visit our page on the 3Ms to eliminate muda.
3. Understanding the Customer and Their Expectations
Another critical aspect of LEAN Management is its emphasis on added value from the customer’s perspective. Rather than focusing solely on internal efficiency, companies must understand what truly matters to their customers and direct their efforts accordingly. Aligning processes with customer needs and preferences allows companies to provide higher-quality products and services while reducing costs. Indeed, knowing customers’ expectations is a great way to adapt production and optimize processes.
4. Implementing Continuous Improvement
LEAN Management is also based on continuous improvement. Instead of seeking one-time solutions, companies must commit to an ongoing process of optimization and innovation. This involves encouraging all employees to contribute new ideas and participate in problem-solving. To facilitate this, SESA SYSTEMS offers a training game for problem-solving awareness with a starter kit to help apply this method effectively in companies. Revisiting even functional systems for potential optimizations is encouraged, using the PDCA cycle, originating from the Deming Wheel.
5. Engaging Leadership
LEAN Management requires total commitment from leadership. Executives must not only actively support improvement initiatives but also be an integral part of the organizational culture. This means taking concrete actions to promote and sustain LEAN at all levels of the company.
6. Enabling Open and Cross-Functional Communication
Transparency and open communication are essential for successfully adopting LEAN Management. Companies should create an environment where information is shared freely, and employees feel comfortable expressing their concerns and ideas. This fosters collaboration and enables the entire organization to work together toward common goals.
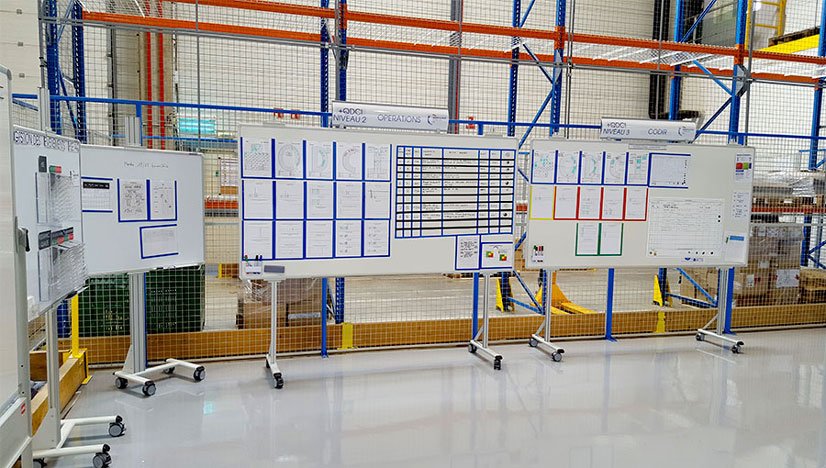
What are the Benefits of LEAN Management?
The potential benefits of LEAN Management are numerous and significant. By reducing waste and optimizing processes, companies can achieve substantial cost savings. Furthermore, by improving quality and reducing lead times, they can boost market competitiveness and increase customer satisfaction. LEAN Management also offers considerable advantages for employees. By eliminating redundant tasks and sources of frustration, it can improve morale and motivation. Additionally, by encouraging employee participation in continuous improvement, it fosters professional development, enhances a sense of belonging, and strengthens team cohesion.
What Are Key Points of Caution?
Despite its many benefits, implementing LEAN Management is not without challenges. It requires time and resource investment, as well as a shift in organizational culture. Additionally, it may be resisted by employees who fear change or have difficulty letting go of established routines. To mitigate these issues, companies should take a strategic and systematic approach. For instance, starting with pilot projects can demonstrate the benefits of LEAN Management and win employee support. Moreover, training and supporting all levels of the organization are essential to ensure successful adoption.
Key Takeaways…
In conclusion, LEAN Management offers a powerful framework for improving operational efficiency and business performance, generating time and cost savings that benefit the organization. By eliminating waste, focusing work on creating customer value, and promoting continuous improvement, it can fundamentally transform how companies operate. While its implementation may pose challenges, the potential benefits are well worth the effort for companies aiming to stay ahead in a constantly evolving competitive business environment.