How to Organize a Stainless Steel Workstation According to Lean Manufacturing Principles?
SESA SYSTEMS: A Recognized Manufacturer of Stainless Steel Workstations
Designing stainless steel workstations is a crucial step in developing an efficient industrial layout within a company. With over 30 years of experience, SESA SYSTEMS offers numerous solutions through its stainless steel products. These workstations, often built with a combination of aluminum and stainless steel structures, provide superior quality while meeting the ergonomic and sanitary standards required in sectors such as food processing, pharmaceuticals, and cosmetics. The various customization options developed during the design process allow employees to adjust the workstation to fit their individual needs, creating a comfortable and efficient workplace. The creation of a diverse range of ergonomic stainless steel workstations addresses the specific needs of various industrial workshops, thus helping optimize operations within the company. By emphasizing ergonomics as a key element of design, these stainless steel workstations integrate smoothly into production processes, enhancing productivity while ensuring worker well-being.
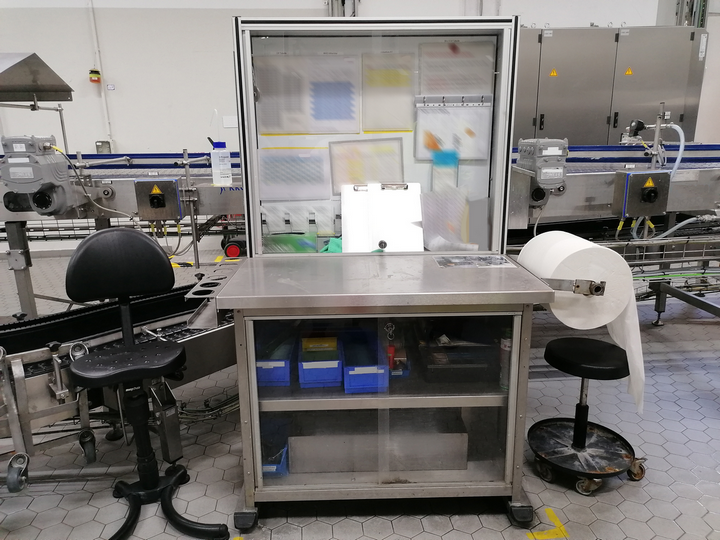
What Are the Principles of Lean Manufacturing?
Lean Manufacturing is a production philosophy aimed at eliminating waste and improving efficiency. The goal is thus a better use and control of the resources of the company. It is based on five fundamental principles:
- Clarify Value for the Customer: This involves understanding what the customer expects from the product or service.
- Identify the Value Stream: This means mapping out the production process, from the customer order to product or service delivery.
- Eliminate Waste: This involves identifying and removing activities that do not add value for the customer.
- Continuously Improve: This principle focuses on establishing a process of continuous improvement to eliminate residual waste.
- Empower Autonomy: This involves providing operators with the necessary tools and autonomy to improve their own work.
Organizing a stainless steel workstation according to Lean Manufacturing principles enhances production efficiency and productivity. It also helps reduce the risk of accidents and injuries, as well as production costs.
How to Apply Lean Manufacturing Principles to Organize a Workstation?
To organize a stainless steel workstation following Lean Manufacturing principles, here are some practical tips:
- Ensure Sufficient Space: Space is essential for proper workstation organization. It should allow operators to move freely and easily access tools and equipment.
- Place Tools and Equipment Within Reach: According to the 5S method, tools and equipment should be positioned so that operators can reach them easily without moving.
- Separate Production Activities: Different production activities should be separated to avoid waste from unnecessary movements and tool changes.
- Use Visual Aids: Implementing effective Visual Management with visual aids like labels and diagrams can help operators orient themselves on the workstation and perform tasks more efficiently.
- Simplify Processes: Processes should be simplified as much as possible to avoid waste related to unnecessary or complex steps. Additionally, displaying these processes visibly helps workers minimize errors.
By following these principles, you can organize your stainless steel workstation to enhance the efficiency and productivity of your production.
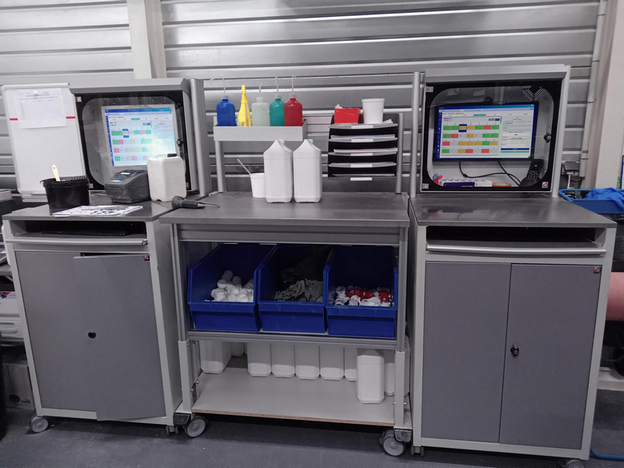
Concrete Examples to Improve Your Stainless Steel Workstation:
- Install shelves or cabinets to store tools and equipment, which will help save space and make tools more accessible.
- Set up carts or mobile trolleys to transport parts and products, reducing the need for operators to move around.
- Use labeling systems to indicate the location of tools and equipment, allowing operators to quickly find what they need.
- Simplify work instructions to make them easier to understand, enabling operators to perform tasks faster and more efficiently.
Key Takeaways
By applying Lean Manufacturing principles to your stainless steel workstation organization, you can save time and money, improve operator safety, and increase customer satisfaction.