How to Implement Continuous Improvement in a Business?
What is "continuous improvement"?
Continuous improvement is a process aimed at constantly identifying, analyzing, and implementing enhancements in all areas of a business or process. This project is often achieved through LEAN Management methods like the PDCA (Plan-Do-Check-Act) cycle, which ensures that changes are both effective and sustainable. By nature, this process has no fixed end date—it should be ongoing and regularly considered. However, specific objectives should be defined to monitor the effectiveness of this process, with progress checked at defined intervals.
Why Implement Continuous Improvement?
Continuous improvement is essential for the long-term success of any organization, regardless of its sector. Whether in manufacturing, business, education, healthcare, or any other industry, establishing a continuous improvement process ensures steady growth, increased efficiency, and adaptability to change. While one might think that if an organization is already performing well, it’s best to leave successful processes unchanged, this is actually the fastest way to fall behind competitors. Here are some core principles for implementing an effective continuous improvement strategy.
Steps to Implement Continuous Improvement
- Integrate Continuous Improvement into Company Culture: First, it’s crucial to foster a company culture that encourages openness to change and improvement. This requires strong leadership commitment and clear communication about the importance of continuous improvement for the entire organization. All employees should be involved. Fear of change, which often reflects a fear of the unknown, is one of the main obstacles to implementing continuous improvement. By encouraging team members to identify improvement opportunities and recognizing their contributions, you empower them to drive change and help create an environment conducive to innovation and growth.
- Define Objectives: Set clear, measurable objectives. Identify priority areas where improvements are needed, and establish performance indicators to assess progress. Each action should be regularly tracked. By setting achievable goals and consistently monitoring results, you can adjust your continuous improvement strategy based on your organization’s evolving needs.
- Engage All Employees: It is important to involve all levels of the organization in the continuous improvement process. Frontline employees often have valuable practical and operational insights and can provide essential feedback for improving existing processes and practices. Encourage collaboration, participation, and teamwork from everyone to maximize the success of your continuous improvement initiatives.
- Use the Right Tools: Employ appropriate tools and methodologies to facilitate the continuous improvement process. LEAN Management techniques such as Six Sigma or Kaizen offer structured frameworks for identifying issues, sources of waste, inefficiency, and non-compliance, and for developing effective solutions to address these issues. Investing in employee training and skill development in these areas strengthens your capacity to successfully implement quality continuous improvement initiatives.
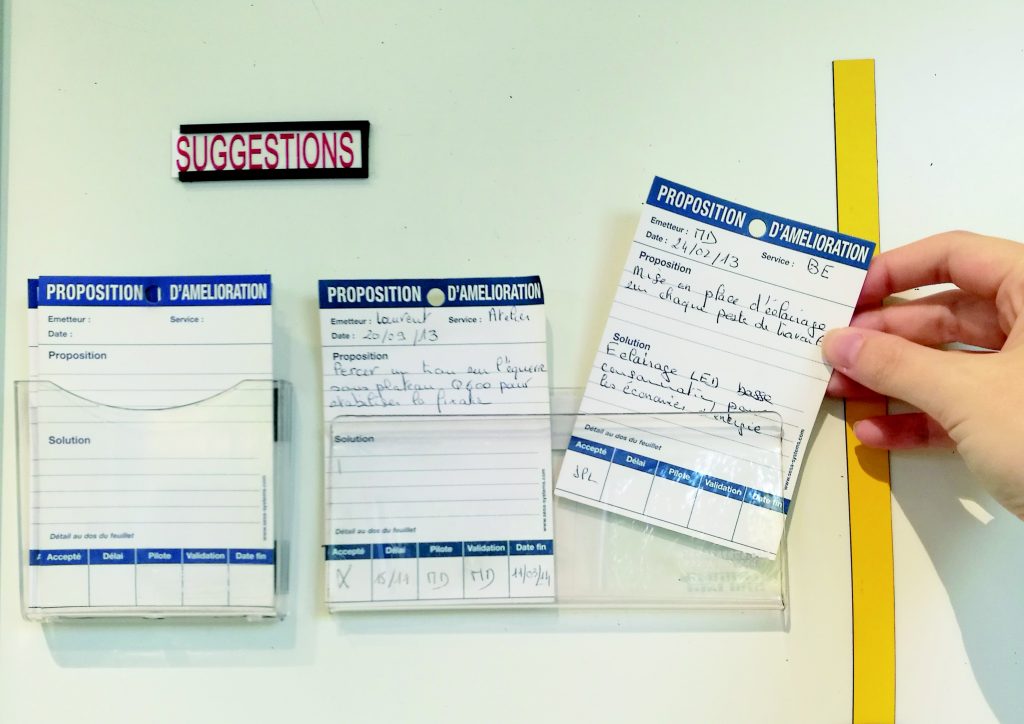
Key Takeaways
Continuous improvement is a critical adaptation process to maintain long-term competitiveness in any organization. By integrating continuous improvement into your organizational culture, setting clear goals, involving all employees, and using the right tools to track process effectiveness, you can enhance the likelihood of establishing this process sustainably and effectively within your organization. Finally, remember that continuous improvement is iterative. Even when you reach your initial goals, it’s essential to keep seeking new ways to optimize operations and meet the evolving needs of your organization and clients. By adopting a proactive approach and remaining open to change, you can sustain a competitive advantage over the long term and ensure your organization’s longevity.