How to Implement LEAN Training in Your Company?
Lean Management is increasingly recognized as an effective model for optimizing processes and improving productivity within companies. A key component of transitioning to a more efficient organization is implementing dedicated Lean training programs. Here are several reasons why integrating Lean into your company is beneficial, along with engaging training methods—such as the APPROACH training games—that facilitate the adoption of this methodology.
Why Choose Lean Management?
Lean Management is much more than a cost-cutting method; it’s a company-wide philosophy aimed at eliminating waste (MUDA), maximizing customer value, and fostering continuous improvement (Kaizen). By incorporating this approach, companies can streamline processes, reduce production lead times, and enhance the quality of products or services provided.
Training Games: A Powerful Tool for Lean Learning
Traditional training can sometimes feel uninspiring and may lack impact. Studies have shown that people learn more effectively when they’re engaged and having fun. This is the foundation for the training games provided by SESA SYSTEMS. Lean Management training can sometimes seem challenging for employees unfamiliar with its principles, but using training games can make the experience enjoyable and engaging. SESA SYSTEMS’ Training Games range offers simple, well-known game variants that allow employees to experience Lean principles firsthand, making understanding and engagement easier.
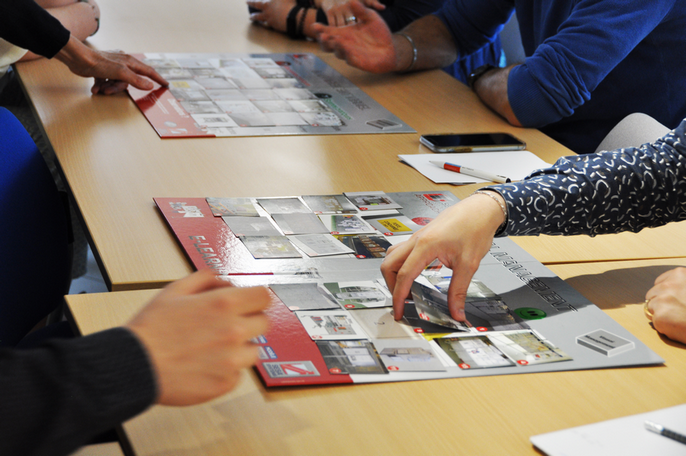
Types of Lean Management Training Games
Various training games can be used to teach Lean concepts. The APPROACH range includes:
- 5S Game – Teaches the 5S method implementation in the company.
- TPM Game – Provides insights into TPM (Total Productive Maintenance) and the importance of preventive maintenance over reactive breakdown management.
- Visual Management Game – Helps employees understand visual management principles and the value of its implementation.
- Hoshin Game – Demonstrates the benefits of actions taken close to the ground level.
- Kanban Game – Raises awareness of effective inventory management and production flexibility through Kanban cards.
- Lean Manufacturing Game – Provides a comprehensive view of Lean production methods.
- Autonomous Team Game – Promotes team autonomy and self-management without frequent manager intervention.
- Kaizen Game – Focuses on the principles of continuous improvement and how to implement them in the company.
- Problem Solving Game – Teaches a structured approach to tackling various organizational problems and difficulties.
- SMED Game – Emphasizes the SMED method and the importance of responsiveness and planning in multi-series production.
- Safety Game – Raises awareness of workplace safety risks and best practices.
- LEAN Office Game – Applies Lean principles specifically to office environments instead of production.
Each of these games encourages experiential learning, allowing participants to understand Lean principles in a concrete and interactive way.
Integrating Lean Training in Your Company Step-by-Step
To incorporate Lean training progressively in your organization, follow these steps:
- Needs Assessment: Identify departments or processes that would benefit from Lean Management improvements.
- Awareness Building: Begin by educating teams on Lean philosophy and its potential benefits.
- Choosing Training Games: Select training games or activities suited to your objectives and organizational structure.
- Gradual Implementation: Use starter kits to introduce training gradually with pilot sessions. Expand company-wide if the results are promising or make necessary adjustments.
- Evaluation and Adjustment: Regularly assess training effectiveness and make adjustments based on feedback and results.
Key Takeaways
Implementing Lean Management training within your company can lead to substantial improvements in operational efficiency and product or service quality. By using tailored training games, you can foster team buy-in for this approach and launch pilot projects with starter kits to measure outcomes effectively, creating an environment that supports continuous innovation and growth.
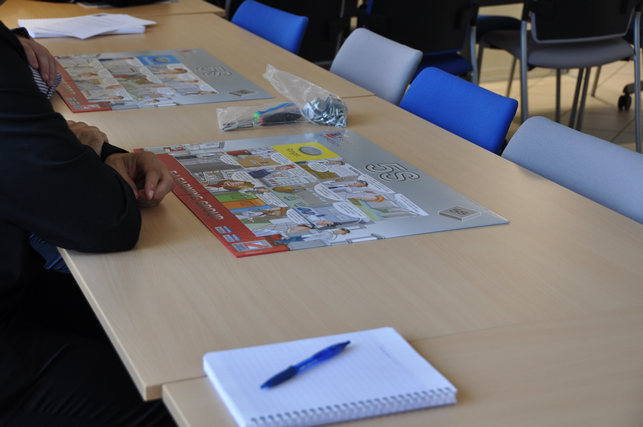