What is Continuous Improvement?
An Exploration of Kaizen, the Deming Wheel and the PDCA Method
Continuous improvement is an essential concept in the field of Lean Manufacturing and Lean Management. It is based on the idea that any company, regardless of its size or industry, must constantly strive to improve in order to remain competitive in the market. We will explore in detail what continuous improvement is, highlighting key concepts inherent to this theme, such as Kaizen, the Deming Wheel and the PDCA (Plan-Do-Check-Act) method.
What is Continuous Improvement?
Continuous improvement, also known as Kaizen in Japan, is a systematic approach to continuously improve processes, products, and services. The main objective of this solution is to optimize the overall performance of an organization, reducing waste (MUDA), increasing efficiency overall or when there is a problem and meeting changing customer needs.
Kaizen: A Pillar of Continuous Improvement
Kaizen, which literally means "Change Good" in Japanese, is at the heart of continuous improvement. He encourages everyone in the organization, from production staff to managers, to contribute to the constant improvement of processes. Kaizen is based on key principles such as engaging everyone, analyzing data, and adopting a proactive attitude towards change. Kaizen therefore implies an idea of gradual and evolutionary change, unlike Kaikaku which corresponds to a brutal change.
The Deming Wheel (PDCA)
The Deming Wheel, also known as the PDCA (Plan-Do-Check-Act) method, is another essential tool for continuous improvement. This method was developed by the renowned statistician W. Edwards Deming and consists of four interrelated steps:
- Plan: In this phase, improvement goals are defined, action plans are developed, and assumptions are made.
- Do: This step involves the implementation of the planned actions. Changes are tested on a small scale to minimize risk.
- Check: Once actions are in place, data is collected and analyzed to assess their effectiveness. This step determines whether the improvement objectives have been met.
- Act: Based on the results of the verification phase, decisions are made to further adjust and improve processes. If the objectives are not met, corrections are made, and the PDCA cycle starts again.
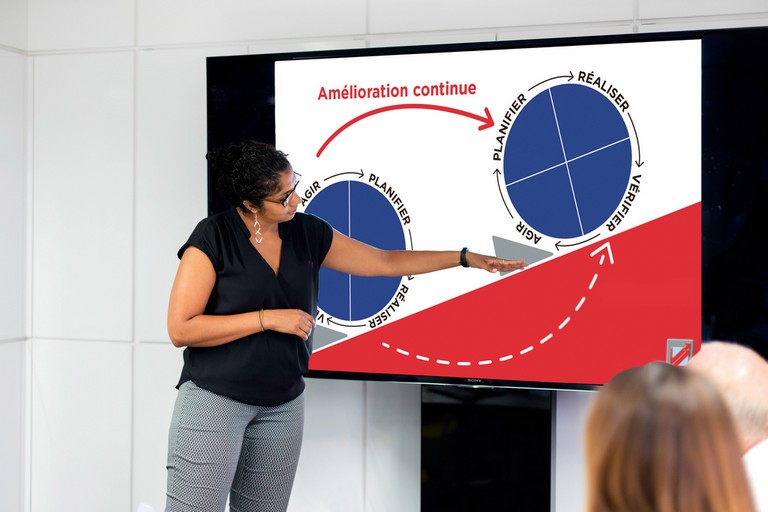
The Benefits of Continuous Improvement
There are many benefits to integrating continuous improvement into a business. This not only optimizes processes and reduces costs, but also increases customer satisfaction, improves the quality of products and services, and strengthens the overall competitiveness of the company. In addition, continuous improvement fosters a positive work environment by encouraging team collaboration, creativity, and innovation.
Implementing Continuous Improvement
To successfully implement continuous improvement in a company, it is essential to follow a methodical approach. Here are some key steps to follow:
- Set clear goals: Identify areas where improvements are needed and set specific, measurable goals.
- Involve all levels of the organization: The commitment of all employees is essential for the success of continuous improvement. Encourage everyone's participation and contribution.
- Collect data and measure: Use data and performance indicators to evaluate the effectiveness of actions taken.
- Analyze and adjust: Based on the results, make adjustments to processes and action plans.
- Communicate and celebrate successes: Keep the entire organization informed of progress and celebrate successes to keep people motivated.
What you need to remember
In conclusion, continuous improvement is a fundamental concept for companies that aspire to remain competitive in an ever-changing environment. By using methods such as Kaizen, the Deming Wheel (PDCA) and following a methodical approach, companies can optimize their operations and time, improve the quality of their products and services, and adapt to the changing needs of their customers. Continuous improvement is not just a method, it is a culture that fosters excellence and innovation at all levels of the organization.