Lean or 5S? Understanding differences and complementarities
In the world of process improvement and quality management, two approaches often stand out: Lean Management and the 5S method. While they share similar goals of efficiency and elimination of waste, they have fundamental differences. In this article, we will explore Lean Management, Lean Manufacturing and the 5S methodology, highlighting their distinct approaches and characteristics and examining how these actions can complement each other in the context of continuous improvement of companies.
Lean Management: A Global Approach to Improvement
Lean Management, also known as Lean Thinking, is a management philosophy focused on maximizing value for the customer while minimizing waste such as, for example, non-quality costs or delays. This approach is based on five core principles:
- Define value: Understand what customers see as value in the product or service.
- Identify the value stream: Identify the process steps needed to create this value.
- Create the flow: Eliminate interruptions and delays in the process to ensure a smooth flow of value.
- Implement a "pull" system: Produce only items when necessary, thus avoiding overproduction.
- Pursue continuous improvement: Constantly seek to eliminate waste and improve processes, including through PDCA.
Lean Management aims to transform the entire company into a value-creating machine, eliminating activities that do not add value for the customer.
Lean Manufacturing: Applying Lean in Production
Lean Manufacturing is a specific application of Lean Management in the field of production. It aims to optimize manufacturing operations by eliminating waste, reducing wait times, and increasing team efficiency. Tools such as the Kanban, the work cells and the SMED (Single Minute Exchange of Die) are often used in Lean Manufacturing to achieve these goals. One of the distinguishing features of Lean Manufacturing is its focus on standardizing processes and reducing variation, which contributes to more stable and predictable production. Thanks to this production philosophy, employees are more versatile, better trained and less prone to MSD risks, which is a significant gain for the company.
The 5S Method: The Organization at the Heart of Improvement
The 5S method is a visual management approach that focuses on organization, cleanliness, and efficiency on the area and workstation. The 5 "S" represent five key steps of the method:
- Seiri (Sort): Eliminate everything that is not necessary in the workplace, keep only the essentials.
- Seiton (Classify): Organize and arrange items in a way that is easy to find and use.
- Seiso: Doing cleaning to maintain a clean and orderly workspace to avoid disruptions and accidents.
- Seiketsu (Standardize): Establish standards and procedures to maintain the first three "S" consistently.
- Shitsuke (Self-Discipline): Encourages adherence to standards and procedures by all employees.
The 5S method aims to create an efficient, safe and pleasant working environment, promoting better productivity and reduced errors.
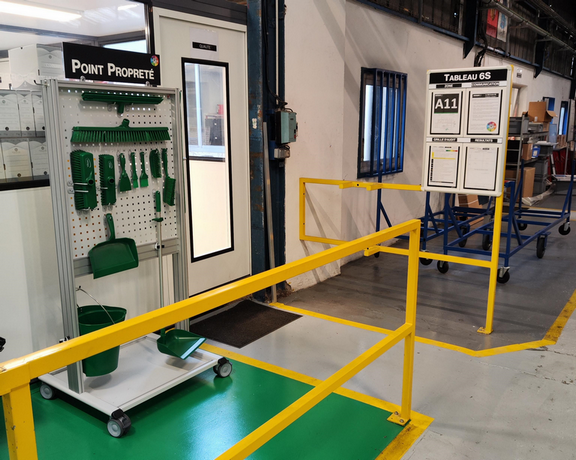
Complementarities between Lean and 5S
Although Lean Management, Lean Manufacturing, and the 5S method have specific goals, they can complement each other. For example, Lean Management provides a comprehensive framework for continuous improvement, while the 5S method offers practical tools and methods for organizing and maintaining the work environment. By combining the two approaches, a company can benefit from an improvement in both its operational processes and its organizational efficiency. If you want to implement a LEAN project in your company, there is a good chance that the 5S method is present in this process. Indeed, 5S is part of the Lean Thinking mentality. Do not hesitate to contact one of our LEAN experts to benefit from personalized support in your project!
What you need to remember
In conclusion, the choice between Lean Management, Lean Manufacturing, and the 5S method depends on the specific needs of your business and the areas you want to improve. However, it is important to recognize that these approaches are not mutually exclusive, and that they can be combined synergistically to create an efficient work environment, reduce waste, and increase customer satisfaction. Ultimately, the key to success lies in the commitment of the entire organization to continuous improvement.