How to eliminate Muda in production and in your processes?
What are Muda?
It is a term of Japanese origin that means waste in French. This term was first implemented in Toyota's production system. When we talk about Muda, we hear about the 3M:
- Muri which means excessive
- Mura which means irregularity
- Muda which therefore means waste
So we are not talking about Muda but about Muda. The elimination of Muda intervenes in the processes of continuous improvement because it prevents the use of disproportionate means for the realization of an operation (Muri), the deviations of realization in particular with the instability of the processes (Mura) and finally it limits the waste (Muda). This method is part of a LEAN process.
Where do the Muda come from and how can it be remedied?
Toyota's desire to eliminate waste comes from the observation that companies were often overproduction and that there was a high production of waste. To limit waste as much as possible, it is not enough to only modify the production part. This is why the 3M appeared, which made it possible to create several steps to be carried out within the company. To eliminate 3M, the use of Lean Management methods is required.
What is Lean?
It is a method of production management that focuses on making the least amount of waste possible, we find at first this method within Japanese companies like Toyota. The Muda intervene in the method of Lean Management called "Six Sigma". It is a Lean Management method that aims to achieve zero defects, it focuses on the customer, his measurement tools and his processes.
The steps of the Six Sigma method:
- Define
- Measure
- Analyze
- Improve
- Control
The goal of this kind of method is to have a fair production, use the necessary time, machines, components and resources. All this is put in place to best meet customer demand while avoiding overproducing and therefore wasting resources that could be useful for other projects.
What methodology should be adopted to eliminate 3M?
Muri:
- Ensure that ergonomics are taken into account before starting any improvements
- Ensure that satisfactory working conditions are maintained
Mura:
- Monitor process stability to improve processes
- An unstable process must be corrected to avoid any kind of waste
Muda:
- Take care of waste as a last resort, because with stable processes and good ergonomic conditions, there is less waste
With the 3M, we can find the 7 Muda wastes , which list the different sources of waste within companies.
Before setting up this waste hunt, it is necessary to first train / raise awareness and present the objectives to employees.
What are the objectives of the 3M?
This method is based on 7 principles:
- Eliminate waste
- Improving learning
- Delay engagement
- Deliver as fast as possible
- Empowering the team
- Integrating quality by design
- Consider the project as a whole
To overcome the 3M, it is necessary to respect an approach. As a first step, it is necessary to check the ergonomics of the workstations. Then, it is necessary to optimize the production using LEAN Management methods. After performing these steps, we can see a decrease in waste (Muda) whether it is a loss of time or loss of raw materials.
The first M (Muri) appears as a result of problems encountered with regard to ergonomics on workstations whether in the office or in the factory. In order to avoid setting up disproportionate means, the 5s method is effective because it aims at the continuous improvement of tasks within companies and workspaces.
The second M (Mura) concerns processes that are not stable, which leads to waste of time or raw materials. In order to remedy this, the VSM method is a good way because it makes it possible to identify the various possible improvements in order to have a certain stability in the processes and therefore optimize production. In addition to VSM, it is wise to use the Jidoka which is an automatic non-conformity detection system, this avoids production errors and saves time on quality verification. On a production line, the VSM method allows a visual representation of the supply, the process... This makes it easier for employees and allows for better performance. The use of the Jidoka facilitates quality control because it detects problems and stops the machine in order to limit waste.
Several LEAN methods fix the last two steps which are Mura and Muda. First of all, the Quick Response Quality Control (QRQC) which reduces unnecessary expenses and waste because the purpose of this method is to treat defects as soon as they appear. Thanks to the QRQC we can integrate quality from the design stage. To reduce waste of time and waste, Takt-Time can be used in addition to the QRQC. The QRQC is a managerial mode because the goal is to raise problems / defects as quickly as possible to his hierarchy in order to solve them as quickly as possible, in addition to this the Takt-time comes to optimize production. Takt-time maximizes production based on seasonality.
What LEAN methods should be used to eliminate Muda?
What are the benefits of LEAN?
- Positively impacts the company
- Working conditions are improved
- Reduces lead times and inventory
- Better transport management
- Optimizes communication
- Production quality is increasing
One of the advantages of Lean is to reduce deadlines and stocks, this is possible with the "Just in Time" (JAT) method. This way of doing things is intended to only order the raw materials at the right time so as not to have too large a stock that could cause waste.
To set up the JAT, it makes sense to use another Lean Manufacturing tool, the Heijunka that makes production smooth and decreases waste by equalizing and planning the activity. The JAT method can also be supplemented by the "Poka-Yoke", which is purely statistical. Poka-Yoke focuses on human error and production process failures. Training through play is a good way to eliminate Muda. Discover our different 5S products such as 5S visual cabinets that allow good ergonomics, mobile services and tray trolleys. Discover our "Training Games" range, in particular via the group training games "HOSHIN Game" and "5S Game".
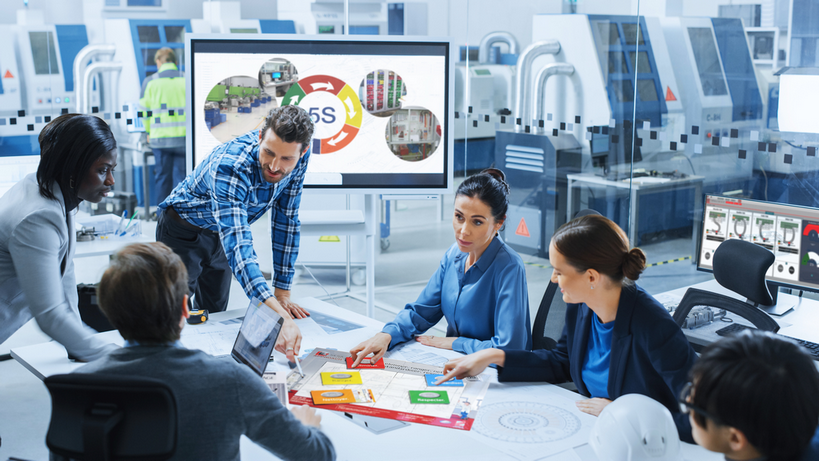