How do you develop and implement continuous improvement?
What is continuous improvement - Kaizen
Continuous improvement is a method of optimising a company's processes and results by reducing errors and malfunctions. This practice consists of identifying problems, finding solutions, and implementing them to continually improve performance and maximise your company's potential. Continuous improvement enables companies to better manage change by creating, improving, modifying, or adapting processes within the organisation.
Why is continuous improvement necessary for businesses?
As we all know, companies must constantly evolve to remain competitive. Customers have increasingly high expectations; competition is fierce, and technology is evolving rapidly. Continuous improvement enables a company to adapt to these changes by identifying problems and finding solutions to improve quality, productivity, and profitability.
Here's a list of the many benefits of continuous improvement in business:
- Improves the quality of products and services
- Reduces costs and waste within the company
- Increases customer and employee satisfaction
- Enables greater operational efficiency
- Improves internal communication and corporate culture
- Improves the company's financial performance and profitability
- Reduces non-value-added tasks
Continuous improvement is a process that is built up over time and is constantly renewed. As you can see, it takes time and commitment to build an effective approach because the improvement must be applicable in order to implement it within your organisation.
Continuous improvement tools and techniques
Continuous improvement is a management tool in the LEAN method, i.e. using resources in the right way to produce a product or service that perfectly meets the customer's needs. Continuous improvement/Kaizen means looking at non-value-added tasks and reducing them to achieve a given objective.
There are many tools available for continuous improvement:
5S Method
It can be applied to all workspaces, the aim of this method is to keep the working environment clean, tidy, and safe in order to optimise the working conditions and environment of employees. It is organised around 5 main stages: Eliminate (remove the unnecessary), Tidy up (a place for everything), Clean up (avoid sources of contamination), Standardise (apply tidiness and cleanliness), Respect (follow and respect together the established rules).
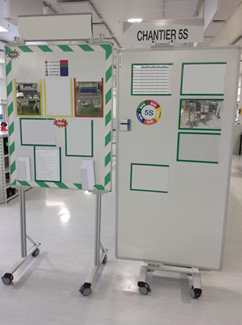
Continuous improvement
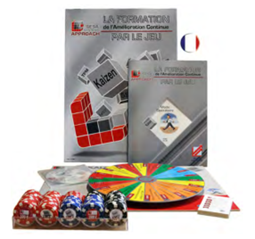
From the manager down to the operators, continuous improvement works through common sense and the involvement of everyone at work. This will make it possible to simplify operational workflows and make small, constant improvements, day after day.
The PDCA method
The PDCA cycle is associated with continuous improvement and is deployed in 4 main stages:
- Plan: situation analysis (existing problems to be resolved are identified and formalised).
- Do: implement the established plan.
- Check: measure the results obtained.
- Act: ensure that the actions last over time.
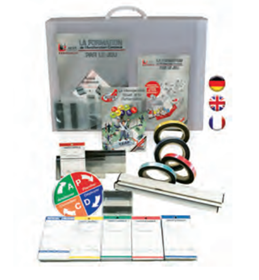
Poka Yoke
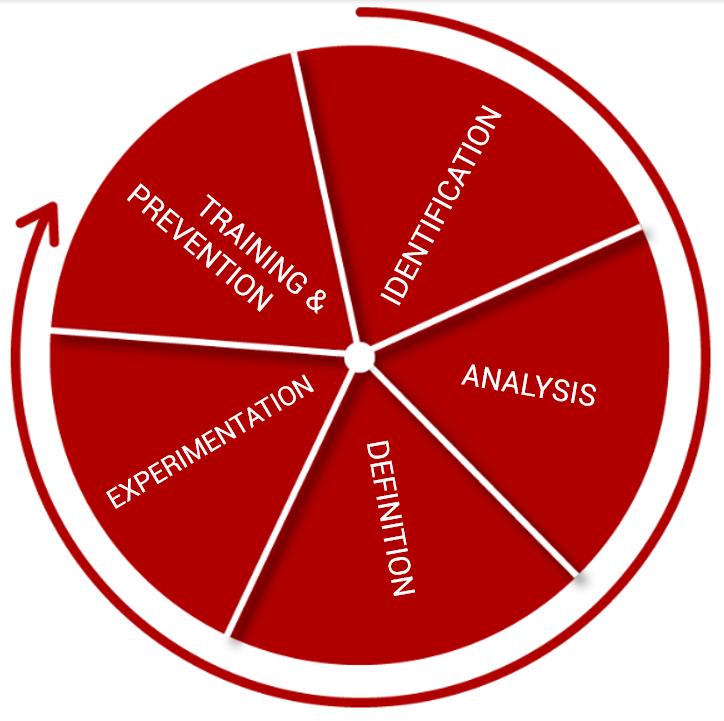
A method of anticipating potential defects during a manufacturing process. It also helps to avoid human errors that could interfere with the process. There are several types of Poka Yoke in the industry: alert, sequential and contact.
Management / Mindset
This technique involves creating ideas as a group, in meetings for example, to solve a problem and develop a solution.
It is important for managers to encourage their teams to adopt continuous improvement methods. If employees are involved and receive positive feedback, they will be more motivated to take part in the company's continuous improvement project and will then be able to communicate their new ideas and participate fully.
Continuous improvement's advice and implementation with SESA SYSTEMS
Implementing a continuous improvement strategy in a company requires a number of steps if we want it to be implemented in the best possible way.
First, it is advisable to make only slight changes, which will be implemented gradually throughout the company. The purpose of the first stage is to test the reaction of the teams to avoid upsetting and disrupting their work routine.
Secondly, the concept of continuous improvement must not become an obsession within the company. Aiming for perfection at all costs would be counter-productive, by creating new problems that shouldn't exist.
Implementing continuous improvement in your company requires total commitment from management and all employees. SESA SYSTEMS can help you implement continuous improvement in your company thanks to the many products related to continuous improvement tools and techniques that we offer.
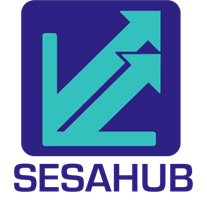
In addition, thanks to SESAHUB, you can improve the overall monitoring of your employees through performance reports on all your connected devices and products linked to Industry 4.0.
Key points to remember
By implementing a continuous improvement approach in your company, you can create a corporate culture focused on reducing non-value-added tasks and improving processes. Employees will feel more involved and will become real actors of change by putting forward proposals.
To find out more about continuous improvement, take a look at our Kaizen guide on our website.